The spirally perforated bullet teeth are a revolutionary advancement in the drilling and cutting industries, merging cutting-edge technology with practical application to deliver outstanding performance. As a product designed to enhance efficiency and effectiveness in drilling operations, these bullet teeth have garnered attention for their unique construction and superior reliability.
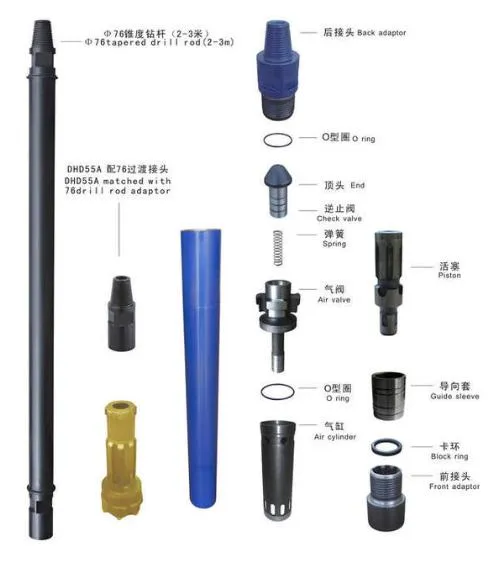
The essence of spirally perforated bullet teeth lies in their design, meticulously crafted to address common challenges faced in traditional drilling and cutting environments. The spiral perforations are engineered to optimize debris removal and minimize clogging, a frequent obstacle that can significantly hinder progress and increase wear and tear on equipment. These perforations facilitate the expulsion of material, maintaining a clean path for continuous operation and boosting the durability of the tool.
Expert engineers have devoted years to perfecting the structure and material composition of these tools. The use of advanced alloys and high-grade steel ensures robustness and longevity under severe operational conditions. In environments where frequent equipment replacement is a major concern, the longevity of these teeth markedly reduces operational costs, a factor eagerly noted by industry specialists.
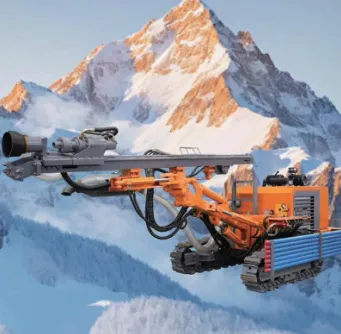
Field experience highly underscores the efficacy of spirally perforated bullet teeth. Operators report increased drilling speed and efficiency, attributing this to the optimized design that requires less frequent manual intervention. The reduced downtime owing to less maintenance indicates a tangible boost in productivity. Experienced professionals value the reduction in effort and time, appreciating how this innovation elevates their capability to meet project deadlines with enhanced precision.
Spiral drill teeth
Moreover, the design is not just practical but also safe. The stability provided by the spiral structure reduces vibration and offers a steadier operation environment. By minimizing operational interruptions and ensuring consistent performance, these teeth not only meet industry standards but frequently exceed them. Having earned certifications from numerous national and international bodies, they affirm their place as industry leaders in safety and compliance.
Trust in these tools is further bolstered by the extensive testing and rigorous quality assurance processes they undergo. Before reaching the market, each batch is subjected to stress tests that simulate real-life conditions, ensuring each unit meets the high standards expected by industry professionals. This dedication to quality reassures operators and stakeholders, ensuring reliability when it matters most.
For companies considering upgrading their equipment arsenal, the spirally perforated bullet teeth represent a worthy investment. They not only enhance operational output but also align with sustainability goals by diminishing material waste and optimizing usage efficiency. Companies focused on environmental responsibility will find this innovation aligns with modern ecological mandates, reflecting a commitment to sustainable practices.
In conclusion, spirally perforated bullet teeth combine engineering prowess with practical application to offer a tool that is efficient, reliable, and sustainable. Their integration into industrial applications promises increased productivity, reduced operational costs, and enhanced safety. As industries continue to seek ways to innovate and evolve, these teeth exemplify how thoughtful design and rigorous testing lead to products that redefine industry standards and expectations. For those in the drilling and cutting sectors, adopting such advanced tools could be the competitive advantage needed to stay ahead in a fast-evolving market landscape.