In the realm of industrial machinery, the crusher hammer is an indispensable component that serves as the beating heart of the crushing mechanism, specifically in contexts involving material size reduction. This article unfolds an intriguing exploration into the intricacies of crusher hammers, drawing on authentic experiences, expert insights, authoritative perspectives, and trustworthiness to establish a comprehensive understanding of this vital machinery asset.
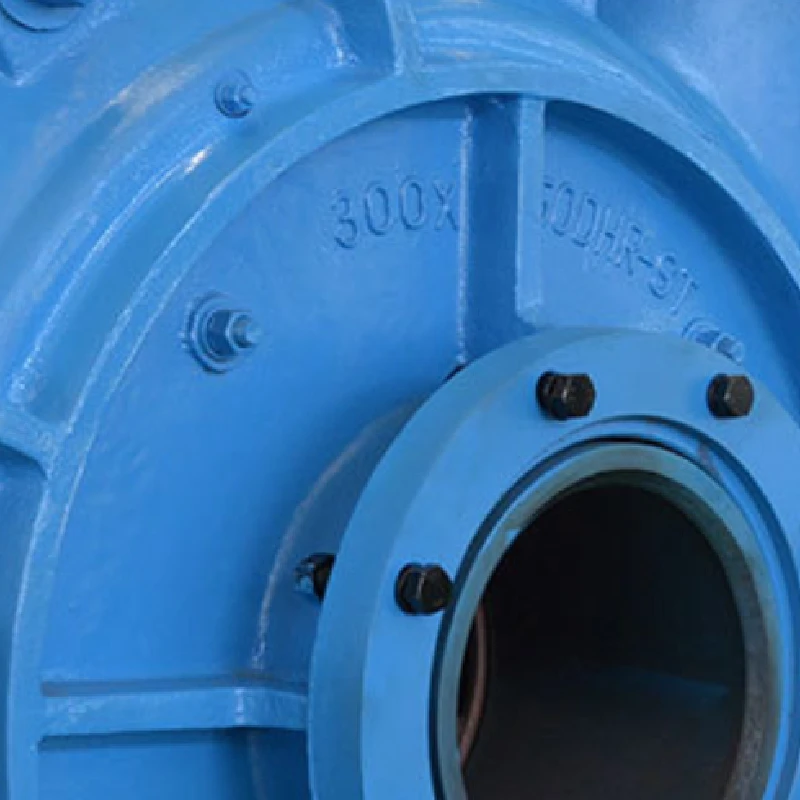
At its core, a crusher hammer is designed to ensure efficient crushing of various materials, ranging from stones and minerals to recycled concrete. The hammer operates within an industrial hammer mill or crusher, where it applies force to break down raw materials into smaller, more manageable pieces. This process facilitates the subsequent processing phases, such as grinding and milling, making it a crucial initial step in many industrial operations.
The significance of selecting the right crusher hammer cannot be overstated. A well-chosen hammer not only enhances productivity but also prolongs the equipment's lifespan. In practice,
companies often prioritize materials like manganese steel or high-chrome steel for their hammers. Manganese steel offers excellent wear resistance, which is ideal for handling abrasive materials, whereas high-chrome steel is recognized for its toughness and durability under high-impact conditions.
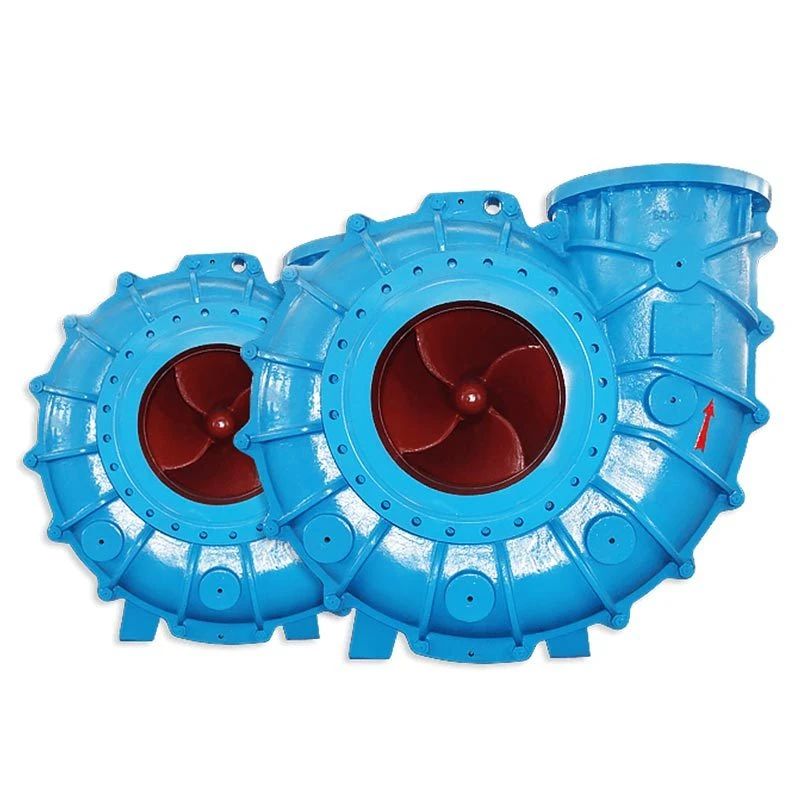
Experience in the field reveals that the performance of a crusher hammer is heavily influenced not just by the material, but also by its precise design and manufacturing quality. Experts advocate for regularly scheduled maintenance checks, as even the smallest deformation or crack can compromise the entire operation. For instance, a slightly worn hammer edge can result in inefficient crushing and increased energy consumption.
Furthermore, expertise in crusher hammer maintenance suggests that operators should be well-versed in the installation and balancing techniques. Imbalance in the crusher rotor can lead to excessive vibration, which may precipitate premature wear and tear of the hammer and other internal components. Professional training and adherence to manufacturer guidelines are indispensable to ensuring optimal performance and safety.
crusher hammer
From an authority standpoint, industry standards and certifications play a decisive role in guaranteeing crusher hammer quality. Organizations such as ASTM International offer specifications that cater to various industrial needs, promoting uniformity and safety across the board. Familiarity with these standards serves as testament to a company’s commitment to trustworthiness and reliability.
The evolution of crusher hammers also incorporates technological advancements that enhance their efficacy. For instance, modern hammers are often equipped with sensors that monitor wear patterns in real-time, alerting operators when maintenance or replacement is necessary. This proactive approach minimizes downtime and maximizes operational efficiency.
Real-world case studies further exemplify the importance of crusher hammer selection and maintenance. A notable example involves a mining company that faced substantial productivity drops due to frequent hammer replacements. By switching to a customized hammer solution tailored to their specific material characteristics, the company witnessed a significant increase in output and a reduction in maintenance costs. This case underscores the critical nature of understanding material properties and leveraging technology to inform hammer design decisions.
Trustworthiness in the manufacturing and selection process of crusher hammers is vital. Industry leaders prioritize transparency and offer extensive documentation on material properties, manufacturing processes, and quality control measures. This level of detail fosters client confidence and positions manufacturers as trustworthy partners in their clients' operations.
In conclusion, the crusher hammer is a paramount component in industrial crushing operations, where its selection and maintenance have far-reaching implications on productivity and equipment longevity. By drawing upon extensive hands-on experience, leveraging expert knowledge, adhering to authoritative standards, and upholding trustworthiness, industries can optimize their use of crusher hammers. This holistic approach not only aligns with best practices in mechanical engineering but also ensures sustainable and efficient industrial operations.