In the world of aggregates and mining, the cone crusher bowl liner stands as a critical component, playing an essential role in the crushing process. This piece may seem insignificant, but it holds significant importance in optimizing production and delivering satisfactory results. This article will delve into the intricacies of cone crusher bowl liners, providing an in-depth exploration grounded in real-world experience, professional expertise, authoritative insights, and the trustworthiness required for making informed purchasing decisions.
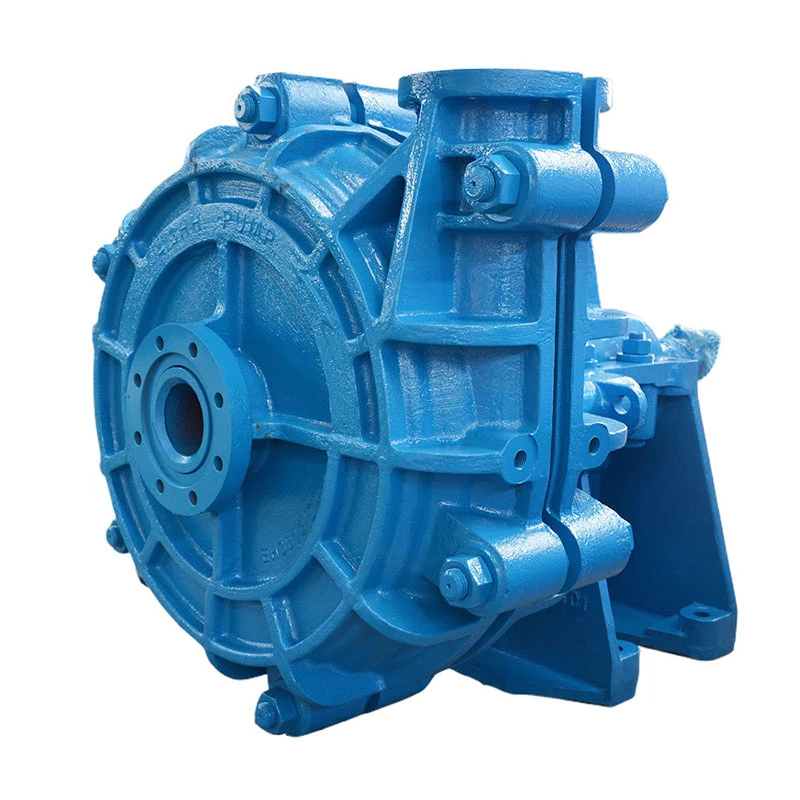
Firstly, a cone crusher bowl liner is a part of the cone crusher that is unique in its design and function. Its primary purpose is to protect the cone crusher from wear, while providing a crushing effect that results in finely reduced aggregate material. Made from high-quality manganese steel for its wear-resistant properties, bowl liners are engineered to withstand the harshest conditions and the constant pressure associated with crushing tough, abrasive aggregates.
From an experiential perspective, operators who have spent significant time in the field will attest to the criticality of bowl liner selection. A well-chosen bowl liner can significantly enhance productivity, ensuring that the crusher can handle large volumes of material without faltering. Conversely, ill-fitted liners not only impair production but can also lead to operational inefficiencies and increased maintenance costs.
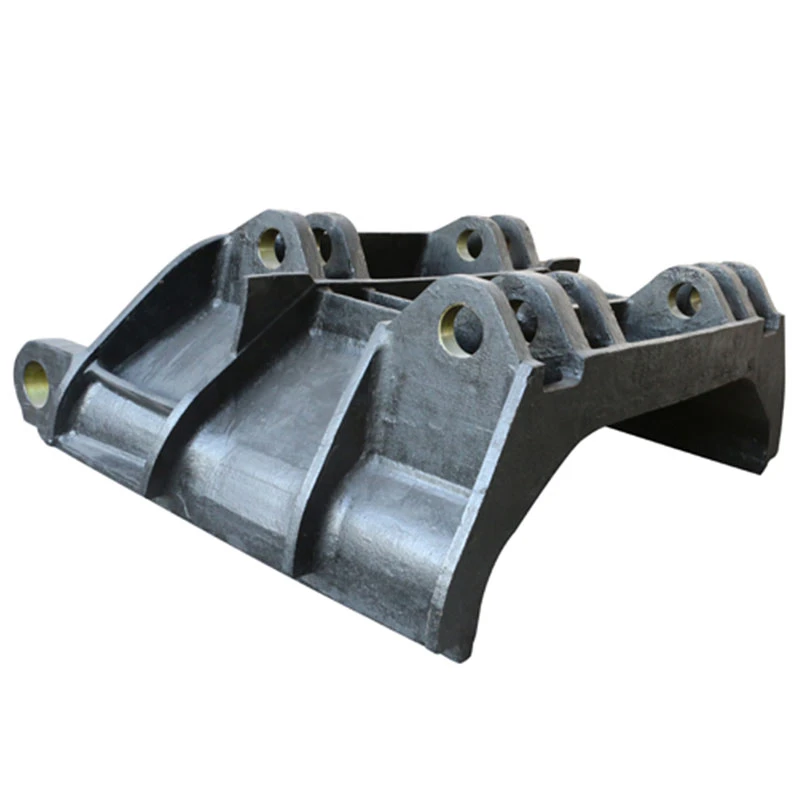
The expertise in choosing the right bowl liner starts with understanding the material being processed. Each type of material has unique properties that affect how it should be crushed. Whether dealing with sandstone, granite, or recycled concrete, the bowl liner must be matched to the material's hardness and abrasiveness. Professionals in the field often rely on historical data and manufacturer specifications to make these determinations, emphasizing the importance of expert-level comprehension of both the curtain settings and the crusher dynamics.
cone crusher bowl liner
Authoritative insights can be drawn from studies and manufacturer guidance, which highlight how different profile shapes, thicknesses, and alloys perform under various crushing conditions. Recent advancements in metallurgy have led to the development of bowl liners that offer extended lifespans, reducing downtime and improving the overall efficiency of the crusher. The introduction of innovations like multi-action technology, which allows liners to accommodate materials ranging from the hardest stones to the softest, binds the principles of engineering with practical application to achieve unmatched performance.
Trustworthiness in cone crusher bowl liner selection is built on the reliability of both the product and the supplier. It's crucial to source from reputable manufacturers who offer warranties and can provide assistance with installation and maintenance. Trustworthy suppliers are those who engage openly with clients, supplying detailed documentation on wear rates, performance statistics, and providing customization options that cater to specific operational needs.
In crafting a cone crusher operation strategy, integrating data analytics has become paramount. Wear sensor technology, for instance, allows operators to predict liner life accurately, enabling proactive scheduling of maintenance tasks. These predictive insights contribute to optimizing crusher availability and reducing unexpected downtimes, further refining the reliability of the operation.
In conclusion, the cone crusher bowl liner, while often overlooked, holds immense potential to influence the efficiency, productivity, and cost-effectiveness of the crushing process. Mastery over its selection and the nuances of its operation draws from a depth of experience, refined expertise, trustworthy manufacturing practices, and authoritative knowledge. For those invested in optimizing their aggregate production, investing in high-quality bowl liners and employing advanced predictive technologies can result in significant long-term benefits. Aspirations for production scalability hinge not just on the machines themselves, but on the pivotal parts that drive their performance, thereby emphasizing the critical role of the bowl liner in achieving crushing excellence.