Portable diesel screw air compressors are game changers in many industries requiring high-performance, reliable, and mobile solutions for compressed air. They are pivotal in construction sites, mining operations, and other fieldwork environments where stationary compressors cannot reach. Understanding the intricacies and best practices for these compressors can significantly enhance productivity while ensuring safety and efficiency.
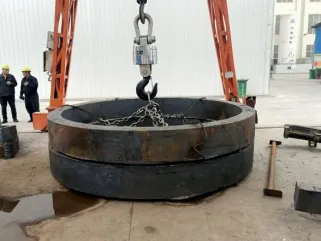
A portable diesel screw air compressor operates using the principle of positive displacement. The air is drawn into the system where twin screw rotors compress it. This design allows for a constant flow of compressed air, which is vital for applications requiring steady output. Unlike their stationary counterparts, these portable units offer the flexibility to move effortlessly across challenging terrains, ensuring that no workspace is out of reach. With diesel engines powering them, they are not reliant on electrical inputs, making them ideal for remote areas.
Expertise in handling portable diesel compressors begins with choosing the right unit for specific tasks. Given the variety of models available, it is essential to select one based on the required pressure (PSI) and cubic feet per minute (CFM) performance. While some users might be tempted to opt for higher capacity units, it is crucial to match the machine with the job's demands to avoid inefficiencies, excessive fuel consumption, or wear and tear. Mastery of this selection process guarantees optimal performance, long-term cost savings, and minimized downtime.
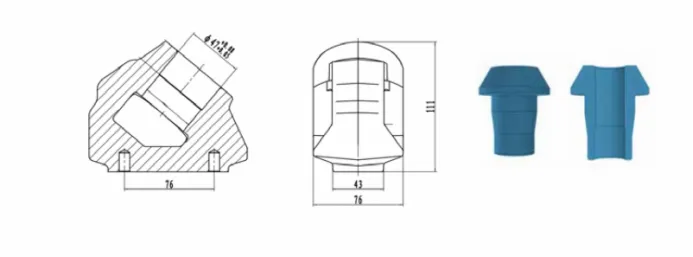
Real-world experience emphasizes the critical role of maintenance in prolonging the lifespan of portable diesel screw air compressors. Regularly scheduled inspections and servicing, such as checking oil levels, replacing filters, and examining hoses for wear, are fundamental. Moreover, diesel engines require clean fuel to function optimally, making it essential to use high-quality diesel to prevent engine knocking and damage. Operators with expertise know that a proactive maintenance strategy not only prevents breakdowns but enhances the reliability and efficiency of the equipment.
diesel portable screw air compressor
Safety is paramount when operating portable diesel screw air compressors. Authoritative sources stress that operators must be well-trained in the equipment's operational procedures. Understanding common warning signals is crucial, such as recognizing unusual noises or reduced pressure output, which could indicate underlying issues. Comprehensive training ensures that operators can perform basic troubleshooting and know when to escalate problems to professional technicians.
Trustworthiness in using these machines can be fortified by selecting products with a proven track record and robust warranty offerings. Established brands often provide excellent after-sales support, ensuring parts replacement and technical support are readily available. Industry certifications and adherence to international standards are additional indicators of a compressor's reliability and quality, reinforcing buyer confidence.
Furthermore, adapting to new technological advancements can greatly elevate the operational efficiency of portable diesel screw air compressors. Modern units are increasingly being equipped with digital control systems, enabling real-time monitoring and diagnostics. These systems not only assist in preventive maintenance but also allow for better fuel management and emissions control, aligning with environmental regulations and reducing operational costs.
In conclusion, portable diesel screw air compressors are essential tools offering unmatched flexibility and performance in various demanding environments. Mastery of these machines involves careful selection, diligent maintenance, and a commitment to safety and quality. By leveraging industry expertise and authoritative resources, users can ensure these compressors deliver reliable, efficient, and cost-effective service over their operational lifespan.