Centrifugal shafts are integral components in various mechanical and engineering applications, their effectiveness stemming from a deep-seated understanding of both mechanics and material science. When examining centrifugal shafts within the realm of product development, several fundamental principles underscore their importance.
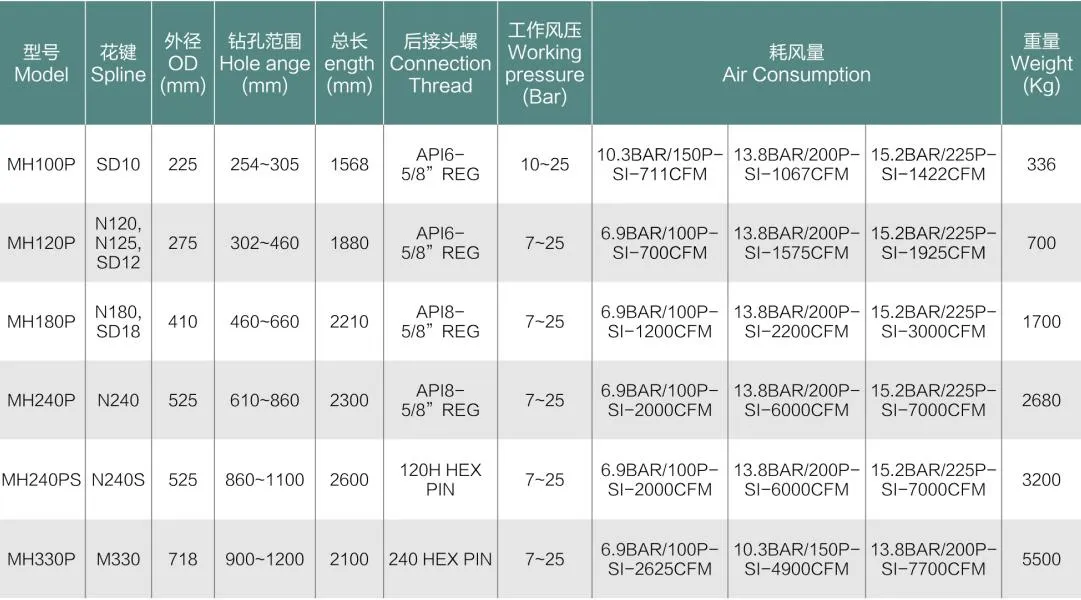
Centrifugal shafts operate in environments where rotational motion is a necessity, functioning at the core of various machines like centrifugal pumps and turbines. These shafts endure immense stress and high speeds, which necessitates precision engineering and materials that can withstand rigorous conditions.
From an expertise perspective, the design of centrifugal shafts incorporates a profound knowledge of dynamics and stress analysis. Engineers meticulously focus on factors such as the material's yield strength, torsional rigidity, and the balance required to reduce vibrations and prolong the machinery's operational lifespan. In most cases, these shafts are crafted from alloy steels with high tensile strength, or composite materials tailored for specific industrial applications. Understanding the interplay of these materials at the microscopic level allows for innovations that enhance the shaft's performance and reliability.
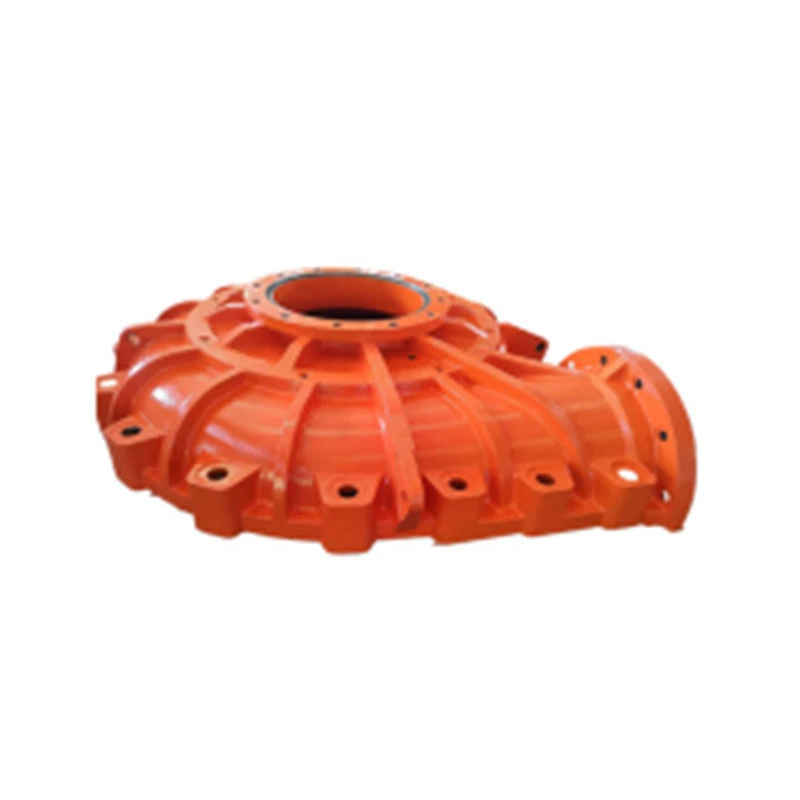
Experience within industry-specific applications further solidifies the operational capacity of these shafts. For instance, in power plants, the precise calibration of centrifugal shafts in turbines can sharply affect energy efficiency and output. Engineers with extensive field experience bring invaluable insights into optimizing shaft design, considering real-world variables like thermal expansion, mechanical loads, and environmental impacts.
centrifugal shaft
Authoritativeness is crucial when discussing centrifugal shafts due to the potential consequences of failure. A well-designed centrifugal shaft not only enhances machine efficiency but also ensures safety. Industry standards such as those from the American Society of Mechanical Engineers (ASME) and the International Organization for Standardization (ISO) provide authoritative guidance on the testing and production of these components. By adhering to these standards, manufacturers reinforce the reliability and safety of their products, thus solidifying their trustworthiness among consumers and professionals alike.
Trustworthiness is at the heart of centrifugal shaft production. Manufacturing companies often undergo rigorous testing processes, including non-destructive testing (NDT) methods such as ultrasound and magnetic particle testing, to verify the structural integrity of each shaft. The data collected from these tests build a foundation of trust with clients, ensuring that each component meets and exceeds the safety margins and performance expectations required by modern engineering standards.
In summary, centrifugal shafts are more than just components within a machine; they are a testament to the intricate blend of scientific understanding and practical application. Their development is underpinned by a wealth of expertise and experience, authoritative guidelines, and rigorous testing to maintain their trustworthiness. As engineering challenges evolve, so too does the design and application of centrifugal shafts, ensuring they remain essential in driving technological progress and efficiency in various industries. As such, individuals and businesses seeking reliable centrifugal shafts should prioritize engagements with manufacturers who demonstrate this commitment to quality, advanced engineering practices, and adherence to global standards, guaranteeing optimal performance and safety.