Selecting the right material for a centrifugal pump shaft is crucial for enhancing pump performance, longevity, and reliability. As the backbone component of the centrifugal pump, the shaft's material influences not only the mechanical integrity of the pump but also its overall efficiency and sustainability under various operational conditions. Here, we delve into the best practices and considerations when choosing materials for centrifugal pump shafts, drawing on extensive industry expertise and practical insights.
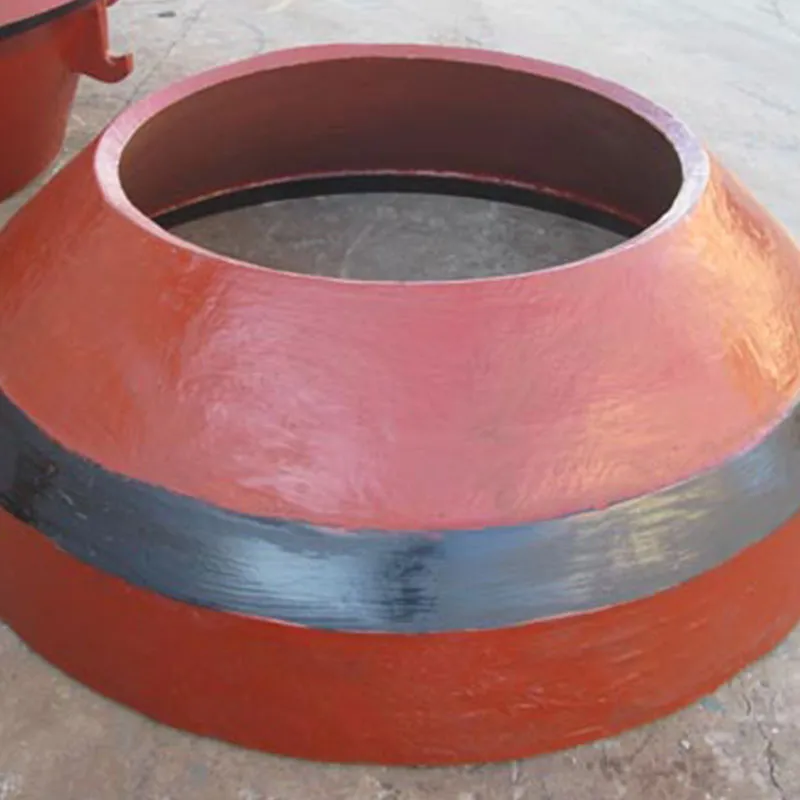
1. Understanding Operational Conditions
The operational environment of a centrifugal pump is paramount in determining the appropriate material for the shaft. Key factors include fluid type, temperature, pressure, and potential for corrosion. For instance, pumps handling corrosive fluids require materials with high corrosion resistance, while those operating at high pressures might demand materials with superior mechanical strength.
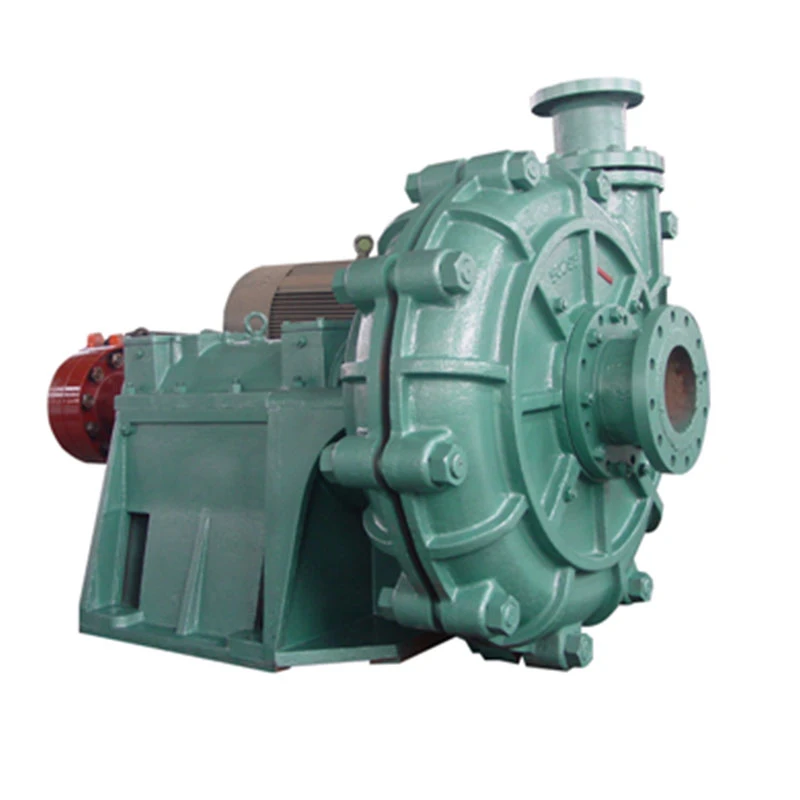
2. Common Materials and Their Benefits
- Stainless Steel A versatile and popular choice, stainless steel offers excellent corrosion resistance and mechanical properties. Grades such as 316 and 410 stainless steel are preferred in environments where corrosion is a concern, such as in processing chemicals or seawater applications.
- Carbon Steel Known for its strength and cost-effectiveness, carbon steel is suitable for pumps operating in less corrosive environments. However, attention to environmental conditions is necessary to avoid potential corrosion issues.
- Duplex and Super Duplex Stainless Steels These are utilized in highly corrosive and high-pressure environments, offering enhanced strength and corrosion resistance. Their dual-phase microstructure provides a balance between toughness and ductility.
- Nickel Alloys In extreme environments involving high temperature and corrosive fluids, nickel alloys like Hastelloy or Inconel are chosen for their exceptional heat and corrosion resistance.
- Titanium Although costly, titanium is chosen for applications where weight reduction is critical, or where extreme corrosion resistance is required, such as in aerospace and desalination operations.
3. Balancing Cost and Performance
centrifugal pump shaft material
While high-performance materials like duplex stainless steel or titanium offer excellent attributes, they come at a premium cost. The decision should balance initial investment against the long-term savings from reduced downtime, maintenance, and enhanced pump lifespan. It’s imperative to conduct a cost-benefit analysis tailored to the specific application needs.
4. Manufacturing Considerations
Manufacturing techniques influence the final properties of the pump shaft. Precision casting, forging, or machining methods can alter material properties such as strength, surface finish, and wear resistance. Selecting a material that responds well to these processes ensures the integrity of the shaft and, consequently, the entire pump system.
5. Real-World Applications and Case Studies
Learning from industry case studies where specific materials were chosen based on their success can offer valuable insights. For example, oil refineries often opt for nickel alloys due to their proven track record in handling sour gas conditions without succumbing to embrittlement or corrosion.
6. Regulatory and Compliance Standards
Adherence to industry standards and regulations is non-negotiable. Materials must meet specific criteria set by organizations such as the American Society of Mechanical Engineers (ASME) or the American Petroleum Institute (API). Ensuring compliance not only safeguards against legal repercussions but also assures stakeholders of the pump’s reliability and safety.
7. Future Innovations and Trends
Looking forward, advancements in material science are paving the way for composites and nano-materials that promise even higher performance. These emerging materials, though still in developmental stages, could offer revolutionary changes in the way pump shafts are crafted and applied, combining lightweight characteristics with unparalleled durability.
In conclusion, the material selection for a centrifugal pump shaft is a critical decision that impacts performance, durability, and cost-effectiveness. By considering environmental conditions, balancing cost with performance, examining manufacturing methods, and adhering to regulatory standards, businesses can enhance their centrifugal pumps’ lifespan and reliability. Staying informed on industry practices and emerging material technologies will ensure optimal shaft material selection and pump operation.