As one ventures into the rugged world of mining, construction, and excavation, the discussion of carbide rock drill bits often takes center stage. Known for their enduring performance and durability, these drill bits are an essential component for anyone serious about rock drilling tasks. In this article, we unveil the intricacies of carbide rock drill bits, integrating real-world experiences and professional insights to demonstrate why they reign supreme when it comes to drilling through the toughest of terrains.
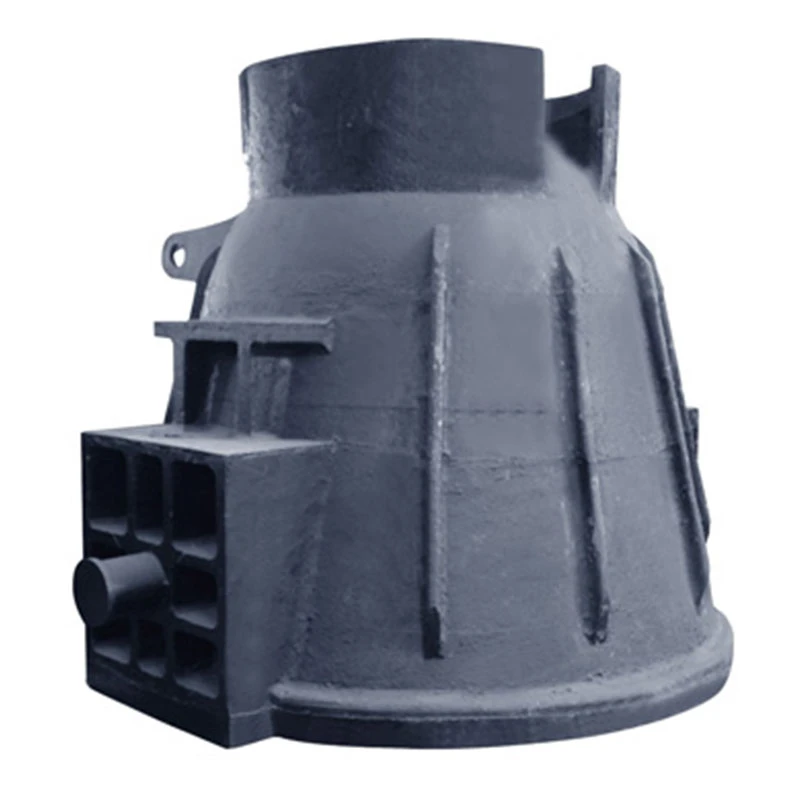
Carbide rock drill bits, an epitome of groundbreaking innovation, are engineered to tackle the harshest of geological challenges. At the heart of their design is tungsten carbide – one of the hardest materials known to man, second only to diamond. This unique composition enhances the drill bits' longevity and effectiveness when penetrating dense rock formations, minimizing wear and maximizing productivity. Through a synthesis of cutting-edge research and industry stories, we shall delve deeper into the anatomy, usage, maintenance, and selection of these formidable tools.
The anatomy of carbide rock drill bits is a marvel of engineering finesse, a subject we explore through a lens of technical expertise. The double-edged sword of strength and precision is sharpened through a strategic metal matrix composition. High-quality carbide tips are often brazed onto steel shanks, forming hybrid supertools capable of enduring immense pressure and high-temperature conditions without succumbing to premature wear and tear. This construction ensures exceptional efficiency in rock disintegration, thus reducing operational downtime and maintenance costs.
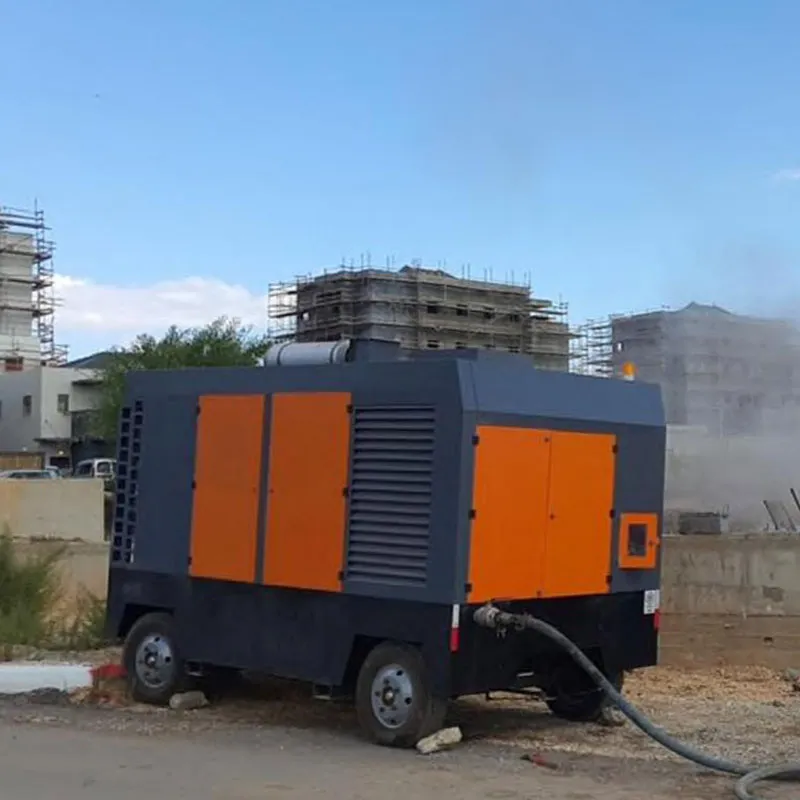
Understanding how to make the most of carbide rock drill bits can elevate project outcomes significantly. Real-world experiences highlight the pivotal role of selecting the appropriate bit design for specific tasks. For instance, button bits are often favored in mining for their superior penetration rates and robust design, while cross bits work wonders in tunneling applications due to their balanced cutting edges. Moreover, drill operators champion the iterative process of assessing rock hardness and adjusting drill bit choices accordingly to enhance bit life and performance.
carbide rock drill bits
Professional expertise further extends into mastering the art of bit maintenance, a crucial aspect often undervalued in the field. Ensuring optimal performance requires regular inspection of the drill bits for signs of wear and chip formation. Using a diamond wheel to resharpen tungsten carbide tips can substantially prolong their operational lifecycle. Additionally, adopting a regimented schedule for checking shank integrity, coupled with adhering to manufacturer guidelines, can prevent costly equipment failures in high-stakes environments.
Exemplifying authoritativeness, reputable sources continually validate the efficacy of carbide rock drill bits in global drilling projects. Leading manufacturers often conduct rigorous field tests under diverse conditions, publishing findings that set industry benchmarks. Case studies from these trials regularly highlight substantial improvements in drilling speeds and precision, reinforcing the decision-making process for enterprises selecting drilling equipment.
Trustworthiness, an indispensable component of credibility, is woven into the fabric of carbide rock drill bit discourse through transparent manufacturing processes and customer feedback loops. Brands that emphasize traceability from raw material procurement to end-product delivery often build stronger connections with end-users. Moreover, user reviews frequently reflect authentic narratives of productivity gains and cost efficiencies, providing relatable insights for prospective buyers.
In conclusion, carbide rock drill bits stand as a beacon of resilience and efficacy in rock drilling domains. Their design intricacies, combined with professional usage strategies, carve a path to exceptional performance in mining, construction, and excavation tasks. By leveraging technical know-how and aligning with industry standards, professionals can harness the superior capabilities of these drill bits to maximize operational success while maintaining cost-efficiency. Through informed choices and meticulous upkeep, carbide rock drill bits continue to earn their rightful place as the quintessential drilling tool in the modern era.