Mud pumps, often referred to as bombas de lodos in Spanish-speaking regions, play a crucial role in a variety of industrial sectors such as oil drilling, mining, and construction. Understanding the nuances of these pumps not only enhances operational efficiency but also extends equipment lifespan, contributing to a more sustainable and cost-effective approach to project management.
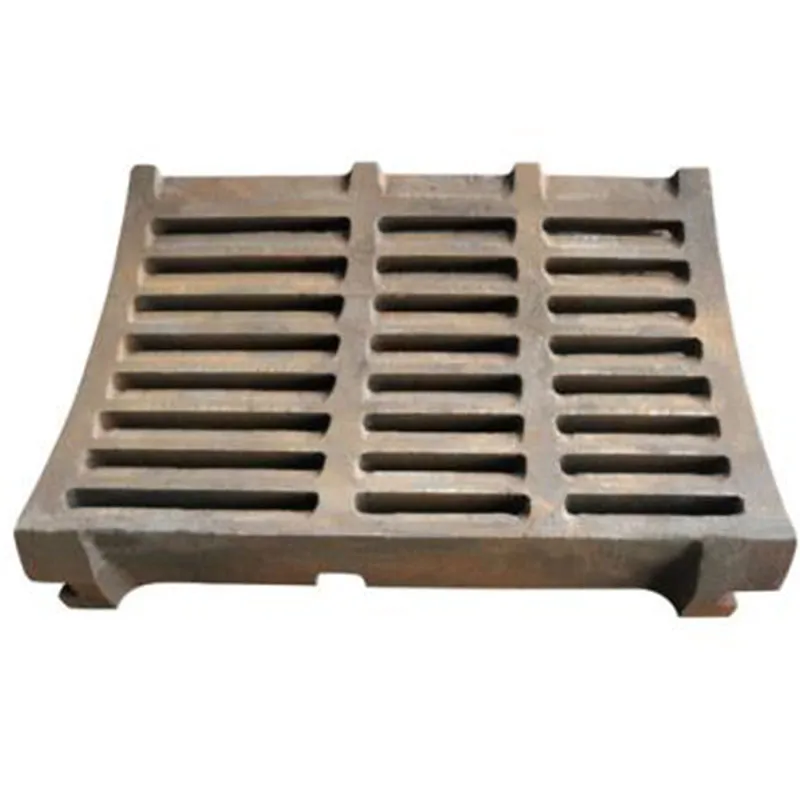
In the oil and gas industry,
mud pumps serve as a backbone for drilling operations. These pumps circulate drilling fluids—commonly known as drilling mud—down the drill string and back up the annulus, carrying with it drill cuttings and maintaining the necessary pressure in the borehole. This process prevents well collapse and facilitates the safe extraction of hydrocarbons. A reliable mud pump directly correlates with successful extraction, minimizing downtime due to mechanical failures. As an industry expert, selecting the right pump involves evaluating factors such as fluid viscosity, pump pressure capabilities, and the Abrasiveness Index of the drilling location.
Mining operations similarly benefit from the efficient application of mud pumps. In slurry transport, these pumps move a mixture of solid particles and liquids across mining sites. Effectively managing the viscosity and density of the slurry plays a vital role in operations, potentially affecting the output, energy consumption, and wear rates of the pump components. Expertise suggests that consistent inspection and maintenance based on operational data can dramatically enhance the lifespan of a mud pump, promoting better productivity and reliability in mining projects.
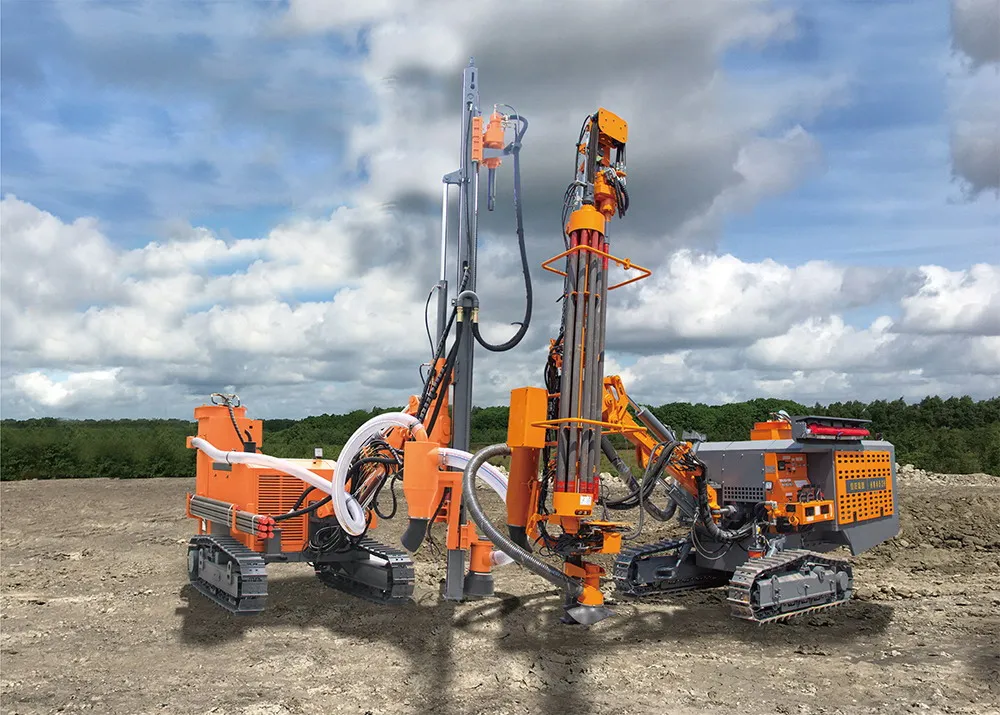
In construction, especially infrastructure projects involving tunnels and foundations, mud pumps are integral to debris removal and maintaining structural integrity during excavation. The adaptability of modern mud pumps to cater to diverse fluid types and debris sizes makes them indispensable. Engineers and site managers emphasize the importance of pump customization to meet project-specific needs, such as adjusting flow rates and incorporating wear-resistant materials to extend pump durability against high-residue fluids.
The need for maintaining pump efficacy and reliability does not end with its operations. Regular training for the personnel involved in operating and maintaining these pumps is paramount. This educational component drives a deeper understanding of the machinery, aiding in the early detection of wear patterns and the implementation of preemptive repairs, thereby mitigating the risk of unexpected breakdowns.
bombas de lodos.
From a technical standpoint, the advancement in materials technology offers new avenues for enhancing mud pump durability and efficiency. The use of high-strength alloys and polymers in pump design has proved effective in combating corrosion and erosion, common challenges faced in abrasive fluid environments. These innovations not only improve pump performance but also foster an environment of safety and reliability across various industries employing these pumps.
Moreover, environmental considerations have increasingly become a focal point in pump design and application. Implementing eco-friendly technologies, such as energy-efficient motors and closed-loop systems, not only strengthens compliance with environmental regulations but also bolsters an organization's sustainability credentials.
Through the lens of authority and trustworthiness, manufacturers and suppliers of mud pumps invest significantly in research and development to deliver products that meet stringent international standards. Certifications and adherence to guidelines set forth by industry bodies enhance a product's credibility, reassuring end-users of its quality and reliability.
In conclusion, understanding and optimizing the use of mud pumps, or bombas de lodos, necessitates a blend of technical know-how, industry-specific insights, and a commitment to sustainability. Employing these pumps effectively ensures operational success across oil, mining, and construction sectors while aligning with broader environmental and economic goals. As technology progresses, the continued evolution of these pumps will undoubtedly drive the industry forward, marking their importance within industrial ecosystems.