In the world of industrial manufacturing, the molino bearing seat plays a critical role in ensuring the seamless operation of machinery and maximizing operational efficiency. As a cornerstone component in mill applications, bearing seats support the rotational movement essential for various processes, making their quality and precision paramount for businesses relying on heavy machinery. This article delves into the technical specifics, importance, and selection criteria for high-quality molino bearing seats, offering insights grounded in industry expertise and built to establish a foundation of trust.
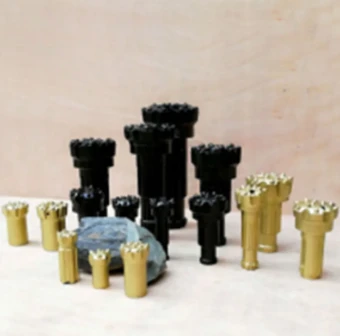
Firstly,
it is essential to understand the anatomy of a bearing seat within a milling setup. Typically, these components are engineered to house bearings securely, ensuring stability and alignment. The primary function of a bearing seat is to support the radial and axial loads exerted by rotating elements, facilitating smooth motion and reducing friction. Precision-engineered bearing seats are crucial for minimizing operational disruptions, which can save significant time and costs related to machinery downtime and maintenance.
Expertise in the field of bearing seat manufacturing reveals that the material composition and design significantly impact performance. Bearing seats are commonly crafted from robust materials such as cast alloys or specialty composites, which offer enhanced durability and resistance to wear and tear. The choice of material should align with the operational environment and the specific demands of the milling process, taking into account factors like temperature variations and exposure to corrosive elements.

For businesses seeking to enhance the efficiency and lifespan of their milling equipment, selecting the right bearing seat is an investment that cannot be underestimated. Expertise suggests evaluating aspects such as load-bearing capacity, compatibility with existing machinery, and the ease of installation and maintenance. Consulting with manufacturers who adopt advanced technologies in designing and testing their products provides assurance of superior quality and reliability.
asiento de rodamientos de molino
Authoritativeness in this domain can be established by examining how well the bearing seat is integrated within broader systems. In many successful industrial applications, upgrades in bearing seat designs have led to marked improvements in productivity. For instance, manufacturers that employ Computer-Aided Design (CAD) software and Finite Element Analysis (FEA) can refine the performance of their bearing seats, reducing potential for failure and ensuring that they perform optimally even under strenuous conditions.
True reliability and trustworthiness in bearing seat solutions are built upon a foundation of comprehensive testing and certification. Providers that adhere to rigorous international standards, such as ISO or ANSI specifications, ensure that their products meet the high-quality benchmarks required for industrial use. Customers can gain peace of mind knowing that each bearing seat is subjected to stress testing and lifecycle analysis before it reaches the market. This level of assurance underpins confidence in the longevity and performance of the product.
Moreover, partnering with reputable suppliers can significantly enhance the overall operational efficiency. Established manufacturers often provide detailed documentation, offering insights into installation procedures, maintenance tips, and troubleshooting, which are invaluable resources for operators. Being supported by a reliable customer service framework allows businesses to address any technical challenges swiftly, contributing to minimized downtime and maintaining productivity.
In conclusion, the asiento de rodamientos de molino is a pivotal element in the realm of industrial machinery. Its significance is underscored by the necessity for precise engineering, the strategic selection of materials, and adherence to exacting standards. Through a commitment to innovation and quality assurance, businesses can leverage these components to not only optimize their milling processes but also extend the operational lifespan of their equipment markedly. In doing so, they position themselves at the forefront of industrial excellence, equipped to meet the growing demands of the modern market.