Enhancing the operational efficiency of machinery is crucial, especially when it comes to critical equipment like a chuck crusher. Properly adjusting a chuck crusher can significantly impact productivity, longevity, and overall performance. Drawing from years of experience in optimizing industrial machinery and adhering to the highest standards of technical expertise, this guide provides essential insights into adjusting a chuck crusher effectively.
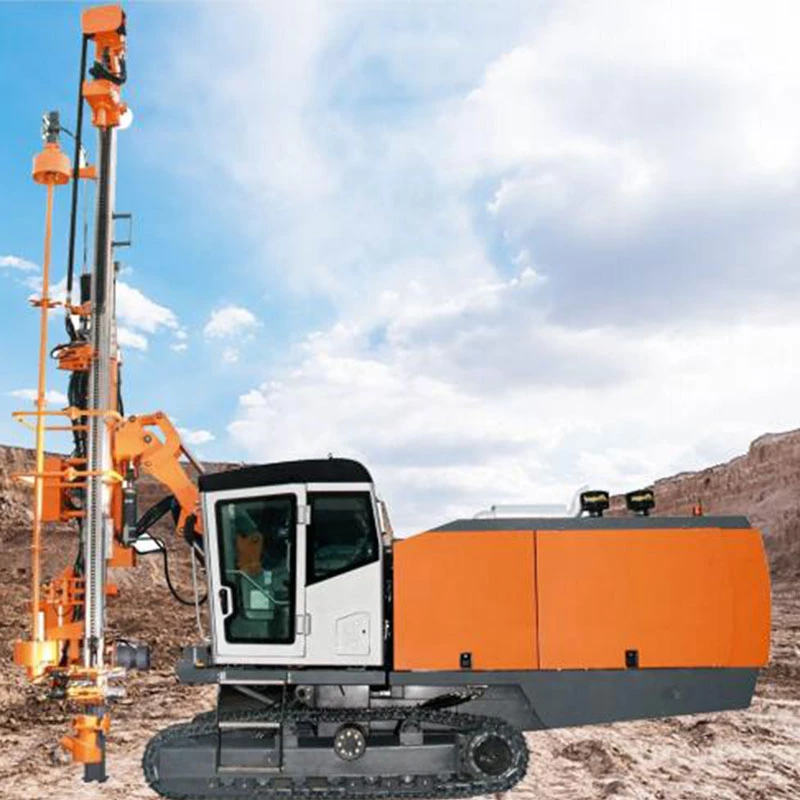
Understanding the Mechanism
Before delving into adjustment techniques, it is imperative to understand the fundamental workings of a chuck crusher. These are essential components in industries like mining and construction, where they are used to break down large rocks into smaller, more manageable pieces. The success of a crusher depends largely on the precision of its adjustments, which directly influences output quality and machine durability.
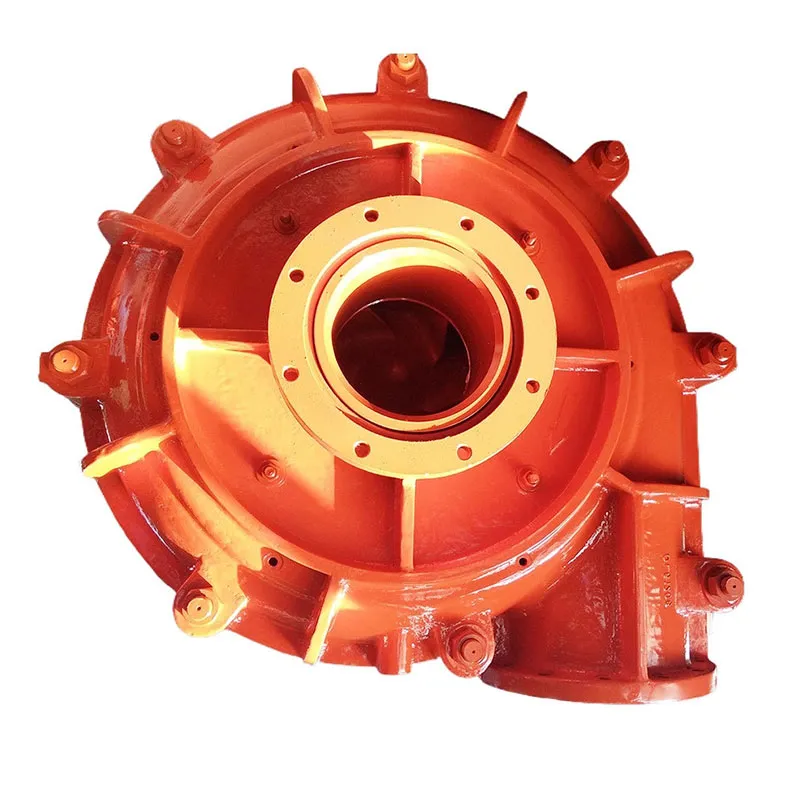
Precision in Adjustment
The accuracy of any adjustment process is vital. Precise calibration of the crusher involves setting the correct gap between the fixed and moving jaw plates. An incorrect gap can result in suboptimal crushing performance and increased wear on the machinery components. Utilizing high-quality measuring tools ensures that adjustments are spot-on and that the equipment operates within its specified parameters.
Technical Expertise in Manual Adjustments
Manual adjustments require a deep technical understanding of the equipment. This involves adjusting toggle plates, ensuring that hydraulic systems are properly aligned, and verifying that jaw plates have the correct symmetry. As an expert, it is critical to pay attention to the manufacturer's specifications and guidelines, ensuring all alterations conform to the prescribed operational standards.
Leveraging Technological Advances
Modern chuck crushers benefit significantly from technological advancements. Automated systems now allow for real-time monitoring and adjustments through computerized controls. Integrating these systems provides a dual benefit it minimizes manual intervention, thus reducing human error, and offers instant feedback on machine performance. Ensuring regular updates to these systems and understanding the software intricacies are essential for maximizing their potential benefits.
ajuste de la trituradora de mandril
Maintaining Optimal Performance
Long-term performance relies heavily on consistent maintenance routines. Scheduled inspections and timely interventions can forestall potential failures. This includes regular lubrication of moving parts, thorough cleaning of components, and replacement of worn-out pieces. Such practices are not merely about maintaining operational efficiency but are also critical in extending the life span of the equipment.
Building Trust Through Authoritative Practices
Building trust with stakeholders and operators relies on maintaining an authoritative approach to equipment handling. Keeping detailed logs of all adjustments and repairs, training staff regularly on updated practices, and adhering to industry standards position your operation as credible and reliable. It’s these practices that separate sophisticated operations from those mired in inefficiencies and frequent downtimes.
A Trustworthy Process
Trustworthiness extends to the quality of the materials and parts used in adjustments. Opting for OEM (Original Equipment Manufacturer) parts or high-quality aftermarket components ensures the machine remains reliable. Furthermore, fostering relationships with reputable suppliers offers another layer of quality assurance and trust, even under the most demanding operational conditions.
Final Thoughts
Excellence in adjusting a chuck crusher lies not just in technical mastery, but also in the commitment to uphold high standards of operational efficiency, safety, and reliability. As the industry continues to advance, the real differentiator will always be the expertise with which these processes are managed and executed, ensuring machinery remains an asset and not a liability.