Drill threads are a crucial component in various industries, serving as the backbone of secure and efficient drilling operations. These threads, which appear deceptively simple at first glance, are a sophisticated engineering solution tailored to meet extremely specific requirements dictated by an array of applications. The realm of drill threads encompasses a wide variety of types, each meticulously designed to enhance the performance, durability, and safety of drilling equipment under distinct operational conditions.
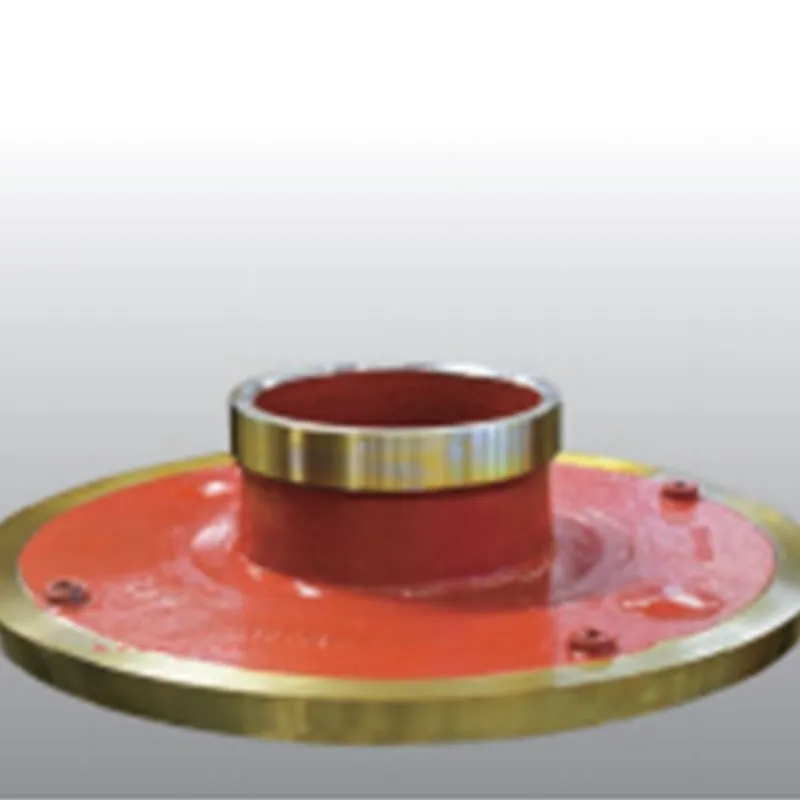
The principal types of drill threads include API (American Petroleum Institute) threads, premium threads, and proprietary threads, each serving unique roles and specifications. API threads are the industry standard, known for their robustness and reliability. These threads are predominantly used in oilfield applications, owing to their capacity to withstand extreme pressures and temperatures. API threads are classified into various categories, such as regular, full-hole, and extreme-line, each with distinctive characteristics to suit different operational needs.
Premium threads, on the other hand, offer enhanced performance features that surpass the specifications of API threads. They provide superior gas-tight seals and excellent torque resistance, making them ideal for challenging applications where standard thread connections might fail. These threads are commonly used in complex drilling operations, such as deep-sea exploration and in geothermal wells, where reliability and protection against leaks and disconnects are of utmost importance.
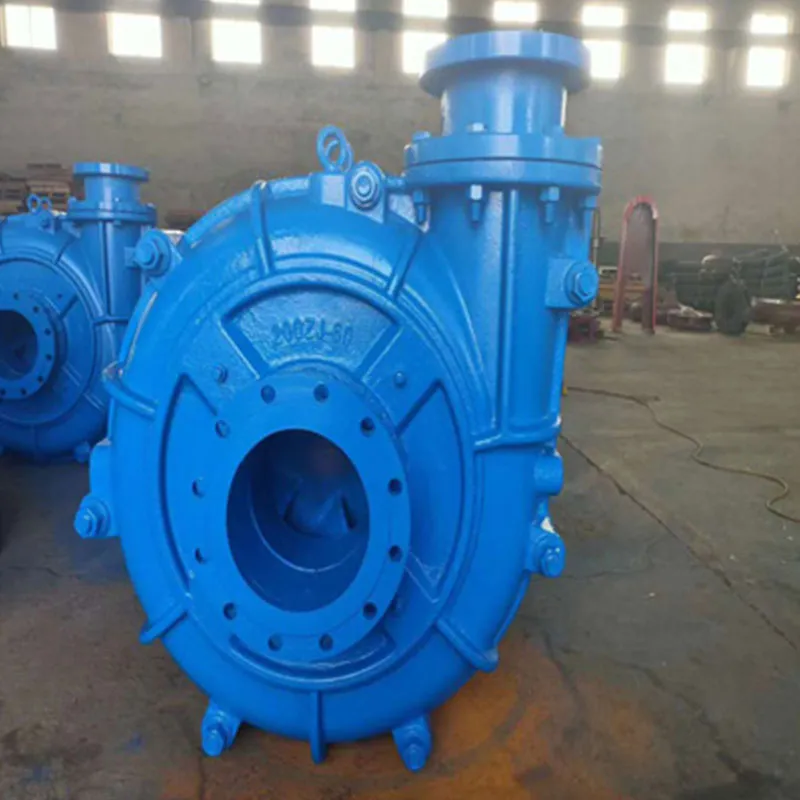
Proprietary threads, as the name suggests, are custom-engineered by manufacturers to meet specific user requirements. These threads often feature unique designs that provide added benefits like increased fatigue resistance and optimised load distribution. Such threads are especially prevalent in situations where standard threads do not provide the necessary performance or longevity, thus offering a tailored solution to unique operational challenges.
Choosing the appropriate type of drill thread involves a keen understanding of the operational environment and the specific demands of the drilling task. Considerations such as the geology of the drilling site, the depth of the well, the type of drilling fluid used, and the expected pressure and temperature conditions play a critical role in thread selection. Furthermore, the compatibility of the thread with existing equipment and standards is paramount in ensuring operational efficiency and safety.
The type of drilling thread
Experience in real-world applications underscores the importance of selecting the right drill thread. In scenarios involving high-pressure high-temperature (HPHT) environments, an incorrect choice might lead to catastrophic failures, including thread damage or even equipment loss. Expertise in drilling operations reveals that threads with superior locking mechanisms and seal integrity are integral to maintaining well control, especially in demanding offshore locations.
Professional recommendations stress that regular maintenance and inspection of drill threads are non-negotiable practices. Detecting early signs of wear and tear, such as sealant degradation and thread deformations, is vital in preventing operational downtimes and costly repairs. The implementation of non-destructive testing techniques, such as ultrasonic testing and magnetic particle inspection, forms a core component of thread maintenance protocols.
The credibility of thread selection is often backed by an adherence to ISO standards and manufacturer certifications, ensuring that the threads not only meet but exceed quality expectations. This fosters trust in their usage across varied applications, from exploratory drilling to production operations.
The dynamic advancements in thread technology continue to introduce innovative solutions that address emerging challenges in the drilling industry. From the development of hybrid threads that combine the strengths of different thread types to the introduction of smart threads equipped with sensors for real-time monitoring, the evolution of drill threads stands as a testament to the industry's commitment to safety, efficiency, and resilience.
In conclusion, an in-depth understanding of the various types of drill threads and their applications is essential for optimizing drilling operations. Leveraging experience, expertise, authoritativeness, and trustworthiness in thread selection and maintenance not only paves the way for successful drilling endeavors but also enhances the longevity and performance of the entire drilling system. As the industry progresses, continued innovation and adherence to high standards will remain pivotal in overcoming the ever-evolving challenges faced by drilling operations worldwide.